The Best Strategy To Use For Alcast Company
Table of ContentsThe Main Principles Of Alcast Company The smart Trick of Alcast Company That Nobody is Discussing9 Simple Techniques For Alcast CompanyGetting The Alcast Company To WorkThe Facts About Alcast Company RevealedThe Greatest Guide To Alcast Company
The subtle distinction depends on the chemical content. Chemical Comparison of Cast Light weight aluminum Alloys Silicon advertises castability by minimizing the alloy's melting temperature level and boosting fluidity during spreading. It plays a crucial function in enabling elaborate molds to be filled precisely. Furthermore, silicon adds to the alloy's strength and put on resistance, making it valuable in applications where resilience is essential, such as auto parts and engine elements.It additionally improves the machinability of the alloy, making it less complicated to refine into completed items. In this method, iron adds to the overall workability of light weight aluminum alloys. Copper boosts electric conductivity, making it advantageous in electric applications. It additionally boosts corrosion resistance and adds to the alloy's overall stamina.
Manganese adds to the toughness of aluminum alloys and enhances workability (Casting Foundry). It is frequently used in functioned light weight aluminum items like sheets, extrusions, and accounts. The visibility of manganese help in the alloy's formability and resistance to fracturing during construction processes. Magnesium is a light-weight aspect that supplies strength and effect resistance to aluminum alloys.
All About Alcast Company
Zinc boosts the castability of aluminum alloys and helps control the solidification process throughout casting. It improves the alloy's toughness and firmness.
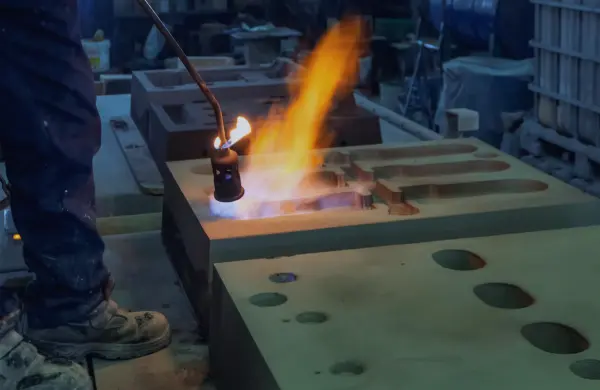
The main thermal conductivity, tensile stamina, return strength, and elongation vary. Select ideal raw materials according to the performance of the target item produced. Amongst the above alloys, A356 has the highest thermal conductivity, and A380 and ADC12 have the cheapest. The tensile limitation is the opposite. A360 has the finest yield stamina and the highest elongation price.
Our Alcast Company Statements
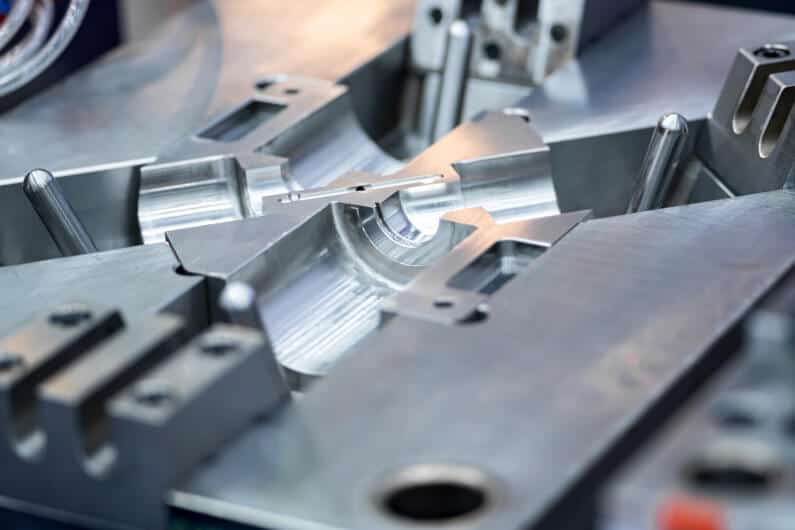
In accuracy casting, 6063 is appropriate for applications where elaborate geometries and high-quality surface area finishes are vital. Instances include telecommunication enclosures, where the alloy's premium formability permits smooth and visually pleasing styles while maintaining structural stability. In the Lights Solutions industry, precision-cast 6063 elements create stylish and efficient lights components that require intricate forms and excellent thermal efficiency.
It causes a finer surface finish and much better rust resistance in A360. The A360 displays exceptional elongation, making it suitable for complex and thin-walled components. In accuracy spreading applications, A360 is fit for industries such as Customer Electronic Devices, Telecommunication, and Power Tools. Its enhanced fluidness permits elaborate, high-precision components like smartphone casings and interaction gadget real estates.
The 30-Second Trick For Alcast Company
Its one-of-a-kind homes make A360 a valuable option for precision casting in these industries, boosting product sturdiness and high quality. Aluminum alloy 380, or A380, is a commonly used spreading alloy with a number of distinctive characteristics. It offers exceptional castability, making it an excellent option for accuracy spreading. A380 displays great fluidness when molten, making sure intricate and detailed molds are properly duplicated.
In precision casting, aluminum 413 radiates in the Customer Electronic Devices and Power Devices markets. This alloy's superior rust resistance makes it an outstanding choice for exterior applications, making sure lasting, resilient products in the stated industries.
Rumored Buzz on Alcast Company
When you have determined that the aluminum pass away casting procedure is suitable for your job, a vital next step is picking the most ideal alloy. The light weight aluminum alloy you select will additional resources considerably influence both the casting process and the homes of the end product. Due to the fact that of this, you must make your choice meticulously and take an educated approach.
Determining the most ideal aluminum alloy for your application will certainly indicate considering a vast variety of characteristics. The first category addresses alloy attributes that influence the production procedure.
Our Alcast Company Diaries
The alloy you select for die casting directly affects several aspects of the spreading process, like just how simple the alloy is to function with and if it is susceptible to casting issues. Warm splitting, additionally referred to as solidification breaking, is a typical die spreading defect for aluminum alloys that can lead to inner or surface-level splits or cracks.
Specific aluminum alloys are more at risk to warm splitting than others, and your option ought to consider this. Another typical flaw discovered in the die casting of aluminum is die soldering, which is when the actors sticks to the die walls and makes ejection difficult. It can harm both the cast and the die, so you ought to search for alloys with high anti-soldering homes.
Corrosion resistance, which is already a noteworthy attribute of light weight aluminum, can vary significantly from alloy to alloy and is a crucial particular to consider relying on the environmental conditions your item will certainly be exposed to (Aluminum Castings). Wear resistance is another residential property frequently sought in light weight aluminum products and can set apart some alloys